A calibração de equipamentos é essencial para garantir precisão, segurança e eficiência em diversas áreas, como indústria e saúde.
Máquinas descalibradas podem causar falhas operacionais, produtos defeituosos e riscos graves à integridade dos colaboradores.
Apesar disso, muitas empresas ainda subestimam sua importância.
Não cometa esse erro, dominando o conceito e boas práticas relacionadas.
Neste artigo, entenda por que investir em calibração é fundamental para o sucesso e segurança do seu negócio.
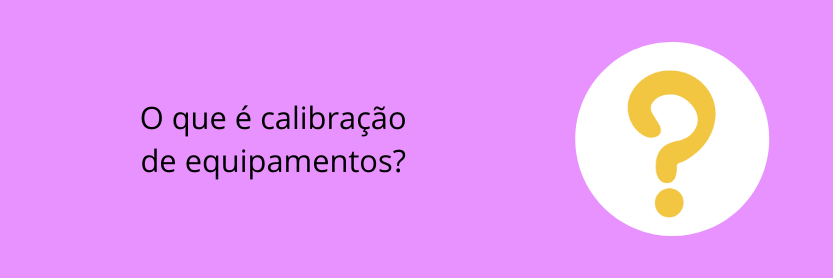
O que é calibração de equipamentos?
Calibração é o conjunto de operações de ajuste, nas quais os parâmetros de funcionamento de uma máquina, instrumento ou equipamento são conferidos e ajustados, se necessário.
Trata-se de um processo em três etapas:
- Verificação: processo que identifica se o equipamento está ajustado
- Calibração: ato de ajustar um equipamento, levando em conta um índice de referência, com base em parâmetros observados
- Ajuste: operações realizadas no equipamento para garantir medições exatas.
Para que serve a calibração de equipamentos?
Uma máquina calibrada é capaz de produzir dentro dos parâmetros ideais de qualidade.
A calibração serve como um pressuposto de excelência, sem o qual não seria possível adequar um processo.
Na indústria de transformação, ela é um elemento indispensável para assegurar que as linhas de montagem se articulem.
A calibração é também um preceito de segurança, do qual depende o desempenho de instrumentos e equipamentos em geral.
Em outras palavras: não há como garantir a integridade em uma operação sem a calibração dos equipamentos envolvidos.
Importância da calibração de equipamentos
A calibração de equipamentos é essencial para garantir precisão, segurança e qualidade em processos produtivos.
Equipamentos calibrados corretamente evitam erros operacionais, reduzem desperdícios e previnem riscos à saúde e segurança.
Em setores como indústria, laboratórios e saúde, a calibração assegura a confiabilidade dos resultados, evita prejuízos financeiros e mantém a conformidade com normas regulatórias.
Não por acaso, há uma série de normas técnicas que preveem a calibração como um procedimento indispensável.
“A organização deve assegurar que o equipamento de monitoramento e medição calibrado ou verificado é usado e mantido, conforme apropriado.”
Na ISO 14001, item 9.1.1 – Monitoramento, Medição, Análise e Avaliação, está a seguinte declaração:
Por sua vez, na ISO 45001, também no item 9.1.1 – Monitoramento, Medição, Análise e Avaliação de Desempenho, é determinado que:
“A organização deve assegurar que os equipamentos de monitoramento e medição estejam calibrados ou verificados, conforme aplicável, e que sejam usados e mantidos como apropriado… A organização deve reter informação documentada apropriada sobre a manutenção, calibração ou verificação dos equipamentos de medição.”
Já na ISO 9001, cuja responsabilidade pela calibração está prevista no item 7.1.5 – Recursos de Monitoramento e Medição, vemos o seguinte:
“A organização deve determinar e prover os recursos necessários para assegurar resultados válidos e confiáveis quando monitoramento ou medição for usado para verificar a conformidade de produtos e serviços com requisitos.”
Quem precisa de calibração de equipamentos?
A calibração de equipamentos é um componente essencial para a indústria em todos os seus níveis.
Da extração da matéria-prima até a distribuição de produtos acabados, não há como assegurar a qualidade sem processos de calibração em conformidade.
Também é uma necessidade, tendo em vista a exigência por garantias de segurança em espaços que ofereçam riscos laborais.
É o caso das linhas de montagem, canteiros de obras e espaços em que máquinas e equipamentos pesados são operados com algum risco à integridade física.
👉 Saiba o que é uma Análise do Sistema de Medição (MSA) e veja como executar e melhorar o sistema!
Como fazer calibração de equipamentos? Confira os 9 passos
Seja qual for o instrumento, equipamento, máquina ou objeto que dependa de certa condição para funcionar, é certo que, cedo ou tarde, ele precisará de ajustes.
No caso da calibração de equipamentos, existem regras gerais, aplicáveis como metodologia para orientar suas rotinas.
Portanto, independentemente do segmento em que uma empresa atue, ela sempre pode se orientar por uma espécie de norma padrão da calibração.
Conheça suas bases a seguir.
1. Identificação
O primeiro passo para desenvolver uma metodologia de calibração é criar meios de identificar os equipamentos sujeitos a esse processo.
Isso pode ser feito por meio de códigos de barras, cores, número de série ou tags, entre outros mecanismos.
O importante é que o equipamento possa ser rapidamente identificável em relação ao seu status, permitindo que seja calibrado no prazo adequado.
2. Faixa de utilização
Determinados equipamentos são utilizados dentro de um espectro de utilização que deve ser alvo permanente de rotinas de calibração.
O exemplo dos pneus pode ser ilustrativo, já que todo fabricante recomenda uma faixa de pressão ideal.
Essa medida varia de acordo com o modelo do veículo, temperatura e peso suportado, entre outros elementos.
3. Preparação do ambiente
Antes que qualquer equipamento seja calibrado, há uma etapa muitas vezes ignorada, mas determinante para a confiabilidade do processo: a preparação do ambiente.
Em laboratórios industriais, onde mínimas variações podem comprometer resultados, preparar o espaço é mais que uma formalidade, mas uma exigência técnica.
A preparação do ambiente consiste em controlar variáveis como temperatura, umidade, vibrações e presença de partículas em suspensão.
Em salas de calibração, por exemplo, os instrumentos de pressão ou massa devem ser mantidos em temperatura constante, geralmente entre 20 °C e 23 °C, com umidade controlada.
O espaço precisa estar limpo, livre de poeira, e com interferência mínima de ruídos ou vibrações mecânicas.
Na maioria dos casos, o controle do ambiente é tão importante quanto a calibração que se faz nele, o que aumenta ainda mais a responsabilidade dos profissionais envolvidos nessa etapa.
4. Seleção do padrão de referência
Em um laboratório de calibração, cada detalhe importa.
Um pequeno desvio pode comprometer a confiança em medições e impactar negativamente a qualidade.
Por isso, a seleção do padrão de referência é uma etapa de extrema atenção no processo de calibração de equipamentos.
Esse padrão funciona como base para comparação, por isso, deve ter rastreabilidade comprovada a um sistema de medição reconhecido, normalmente vinculado a institutos nacionais ou internacionais.
A escolha do padrão, por sua vez, depende do tipo de equipamento a ser calibrado, da faixa de medição e da precisão esperada.
Por exemplo, para calibrar um termômetro clínico, é necessário usar um padrão térmico com incerteza menor do que a do termômetro testado.
5. Realização da medição comparativa
No universo das medições e da calibração de equipamentos, a precisão é tudo.
Seja em um laboratório de testes, em uma linha de produção ou em um sistema industrial, a capacidade de um equipamento fornecer resultados confiáveis depende de uma calibração meticulosa.
Entre as várias fases desse processo, uma das mais delicadas é a realização da medição comparativa, fundamental para garantir que os instrumentos de medição se alinhem com padrões reconhecidos.
A medição comparativa é, basicamente, um processo de confronto entre o equipamento a ser calibrado e uma referência conhecida e comumente aceita.
Esse padrão pode ser um dispositivo com precisão garantida que atua como base para ajustar os instrumentos em questão.
A ideia aqui é verificar como o equipamento sob calibração responde em comparação com a referência.
Assim, os técnicos podem ajustar as leituras do equipamento, assegurando que os valores registrados estejam dentro de um intervalo aceitável de erro.
6. Cálculo do erro e verificação de conformidade
Todo processo de calibração deve levar em conta a tolerância máxima e mínima para o parâmetro adotado.
É um conceito similar ao de desvio padrão em estatística, segundo o qual um parâmetro será considerado aceitável ou dentro da normalidade desde que esteja em certa faixa.
A definição de um limite de tolerância é essencial para definir padrões de qualidade.
Por exemplo: em uma indústria que fabrica alimentos, uma embalagem de 500 gramas pode ter um limite de 0,5 gramas para mais ou para menos, e ainda assim será considerada apta para o consumo.
Assim se faz o cálculo do erro, etapa que precede uma outra de extrema importância na calibração de equipamentos, a verificação de conformidade.
Nela também se calcula o desvio máximo, unidade de medida que determina o desvio aceitável para os equipamentos usados na produção.
Existe inclusive uma fórmula para calcular esse desvio:
- Desvio = Tolerância aceita / Fator (mínimo de 3, mas varia conforme a exigência do processo).
Finalmente, depois de realizado o cálculo do erro, parte-se para a verificação da conformidade.
O que se faz aqui é comparar os desvios obtidos com os limites de tolerância aceitáveis e avaliar a incerteza de medição, o que pode ser feito com fórmulas estatísticas simples ou softwares.
7. Emissão do certificado de calibração
Antes que qualquer balança, termômetro ou instrumento de medição vá para uso prático, é necessário garantir que seus dados estejam alinhados com padrões confiáveis.
É nesse contexto que entra uma etapa indispensável: a emissão do certificado de calibração, que ocorre após a calibração propriamente dita.
O documento funciona como um histórico técnico e legal do instrumento, permitindo que empresas, auditores e técnicos saibam qual o comportamento do equipamento no momento da calibração.
O certificado deve conter as seguintes informações:
- Identificação do instrumento: número de série, marca, modelo, e outros dados que permitam individualizar o equipamento
- Identificação do cliente: nome da empresa ou pessoa que solicitou a calibração
- Dados do laboratório: nome, endereço, número de acreditação (se aplicável), e nome do técnico responsável
- Data da calibração e, se aplicável, a data da próxima calibração recomendada.
8. Sinalização do equipamento
Outra etapa que faz diferença tanto para a rastreabilidade quanto para o controle interno é a sinalização do equipamento.
Ela consiste na aplicação de etiquetas, lacres ou marcações visuais diretamente no equipamento calibrado, informando que aquele instrumento passou por calibração em uma data específica e está, dentro dos critérios definidos, apto para uso.
Essa identificação pode conter dados como o número do certificado, o nome do responsável técnico, a próxima calibração e qualquer observação relevante.
Pode também constar outros dados sobre a calibração como data, validade e situação, caso o equipamento seja aprovado.
E se reprovado, ele deverá ser sinalizado como “fora de uso” ou mesmo retirado de operação.
9. Frequência de calibração
Finalmente, a calibração deve ser feita na frequência adequada, para garantir que o equipamento continue operando ininterruptamente dentro dos padrões ideais.
Essa é uma parte fundamental das rotinas de manutenção preventiva, considerando que certos equipamentos estão mais sujeitos a desgastes prematuros do que outros.
Saiba mais sobre gestão da qualidade
A calibração de equipamentos é uma das práticas de rotina na gestão de qualidade total (GQT).
Ela demanda ferramentas e técnicas específicas que, como tais, geram resultados melhores quando utilizadas por profissionais qualificados.
Essa qualificação você consegue nos cursos Black Belt e Green Belt da Escola EDTI nas modalidades presencial e EAD.
Venha para a instituição de ensino pioneira em Lean Six Sigma no Brasil e faça parte do seleto grupo de líderes que estão à frente das grandes empresas do mercado.
Conclusão
A calibração de equipamentos é um terreno vasto, no qual cada área define suas rotinas e parâmetros.
Para ser um profissional dessa área, é fundamental conhecer as normas da ABNT, bem como as normativas ISO.
Além disso, é preciso investir em formação em metodologias de controle de qualidade, como a Lean Six Sigma.
Na Escola EDTI, você se capacita para ser um profissional de destaque, com cursos presenciais ou em regime EAD, com certificação pelo The Council for Six Sigma Certification (CSSC).
Amplie seus horizontes, baixando totalmente grátis um e-book sobre as 7 Ferramentas da Qualidade.